Gain critical insights with trusted quality information, technology and scientific expertise
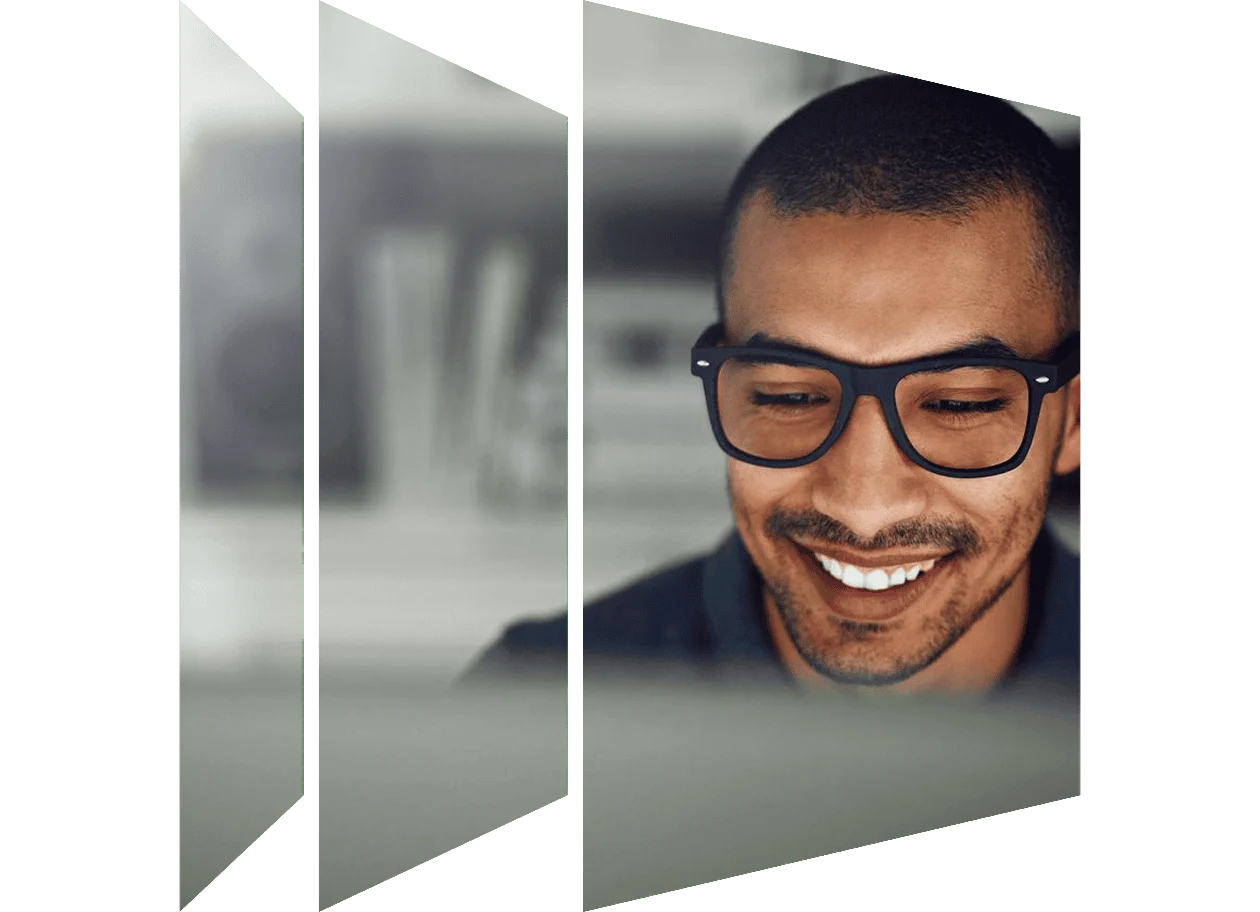
Facing pressure to innovate quickly and champion sustainability, chemicals and materials companies trust Elsevier to transform complexity into clarity.
Make informed decisions at critical moments in the innovation process based on:
Trusted quality information, including peer-reviewed scientific literature and chemistry data
Innovative technology that powers data transformation and analytical and predictive tools
Domain and data science expertise to solve complex problems with data solutions for R&D
Let's shape progress together.