In chemical engineering, the right knowledge improves process safety
January 25, 2022
By Jim Harper
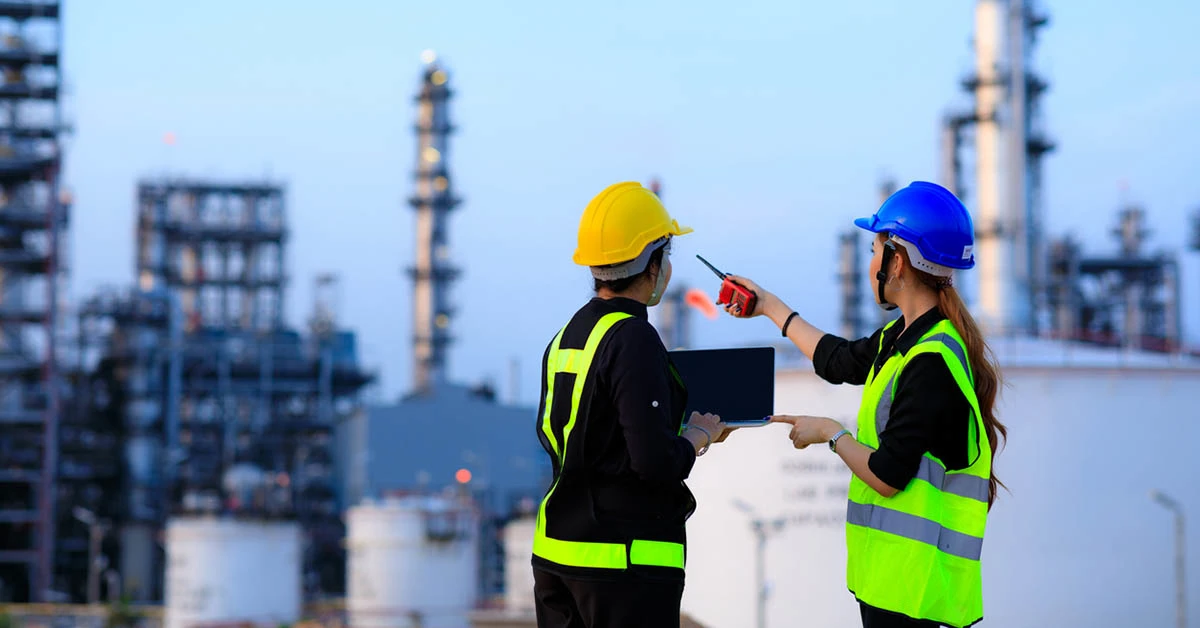
A process safety engineer gives tips to identify hazards in your company’s chemical processes and develop a risk assessment strategy
Professionals in energy, petrochemicals, the chemicals industry and similar fields do a great job day in and day out looking after the many aspects of safety. But when things go wrong, the consequences can be grim. Consider incidents such as the explosion at the Grangemouth refinery in Scotland in the 1980s, the Deepwater Horizon oil spill in 2010 or the Fukushima nuclear disaster of 2011.
In each case, planning, process and equipment faults led to dire consequences. And in each case, a thorough risk assessment probably could have identified hazards, isolated root causes, and suggested remedial efforts that may well have reduced the severity or even prevented these tragedies.
“An effective hazard identification strategy allows you to thoroughly identify risks and make appropriate decisions around prioritization and mitigation,” said Kathryn Grant, Process Safety Engineer for Icarus-ORM, in a webinar hosted by Knovel: Strategies for Chemical Process Hazard Identification.

Kathryn Grant
Hazard identification and risk assessment can begin with simple what-if scenarios. This is a good way to start. It’s relatively easy to do and can lead to rewarding brainstorming sessions.
But beyond this, more systematic planning is crucial. The lack of a systematic approach opens the door to the omission of vital safety and process scenarios.
A hazard and operability study (HAZOP) is often a better way to evaluate risk. By offering structure, a HAZOP makes it possible to break risk down into nodes, deviations and causes and take into account a wider range of potential scenarios. Still, it remains difficult to identify all possible hazards via a HAZOP, particularly when the people involved have a poor understanding of the process, when the organizational culture inhibits safety efforts or can lead to division between competing groups, or when dealing with complicated processes.
Dealing with complex processes
Complex processes and convoluted flow paths that weave their way through a great many pieces of equipment can challenge the work of safety and risk specialists, especially when toxic or flammable materials are involved. In these situations, it often makes sense to break things down into smaller and more manageable pieces.
For example, the process may be high pressure in one stage and low pressure in another. A small leak may be of little consequence in the low-pressure unit but potentially catastrophic in the high-pressure unit. A risk assessment, then, should carefully examine each operating mode.
As Grant explained:
A poor understanding of the process can lead to inadequate preparation or risk assessments being performed at the wrong time. A clear understanding of the process is one of the most critical components of hazard identification and risk mitigation.
Therefore, it’s vital to understand all relevant parameters. Those conducting risk assessments must take into account factors such as pressure sources, operating and design conditions, the connections among systems (such as piping, valves and couplings), and points where processes break from high- to low-pressure.
The repercussions from serious incidents must also be considered. This entails a review of the properties of products, their explosive or toxic capabilities, and the location of the facility. Premises close to residential buildings or major roads with large numbers of onsite personnel have a completely different risk profile than an unmanned plant in a remote region.
All these factors must be evaluated by the risk assessment team. Unfortunately, the wrong people may be invited to attend process safety meetings. Alternatively, there can be too many people present or too few. The key is to gather just the right mix of experts and stakeholders so every voice can be heard, no one is drowned out, and all areas of input and expertise can have their say. A process hazard analysis (PHA) facilitator, a process engineer, an operator, an instrumentation specialist and a project manager, for example, could potentially offer the right number and mix of viewpoints to adequately span the many elements of process risk.
The right knowledge improves process safety
Grant pointed out the various ways faulty information can get in the way of risk assessment.
“Acting on incorrect data such as poor or outdated documentation can hinder risk assessment,” she said.
Accurate information underlies the entire risk assessment process. Take the case of a refinery in Southern Europe producing polyolefin, olefins and catalysts for PE, PP and Polybutylene. The risk assessment team decided to create a plan to reduce accidents by an order of magnitude. They
used Knovel to find in-depth information on the correct distribution of gas detectors and the causes and consequences of previous accidents in other companies related to loss of process containment. What proved especially helpful was being able to access the same knowledge all over the world, including expert AIChE and CCPS content.
By harnessing Knovel, the chemical process group increased its understanding and knowledge of process safety. As a result, an initiative to prevent loss of containment decreased the statistical chance of incidents from a frequency of occurrence of one every 10,000 years to a frequency of occurrence of one every 100,000 years.
Another example of process safety improvement concerns anhydrous sulfuric acid corrosion in stainless steel tanks. In a 300-person complex that produces polymer resins, the process management engineer working was tasked with improving the overall safety of the manufacturing section. The big challenge here was the presence of dangerous and toxic chemicals in confined spaces. This could pose a serious health risk if not addressed properly. A safety review identified the various confined spaces, assessed and scored their level of danger, and created standard procedures to address potential issues.
The Knovel critical database armed the process management engineer and the risk assessment team with accurate data, including chemical processes quantitative analysis, solvents, fire safety codes, pressure relief design, CAS numbers, chemical properties, room concepts, equipment types and more. This know-how enabled the engineer to create a detailed matrix to evaluate the risk associated with a number of small areas. In addition, opportunities were found within the CCPS and AIChE guidelines to further expand the matrix. The team’s work on these issues also isolated simple and inexpensive upgrades that improved the safety of electrical cabinets.