Avoiding corrosive combinations in equipment and infrastructure design
July 20, 2021
By Jim Harper
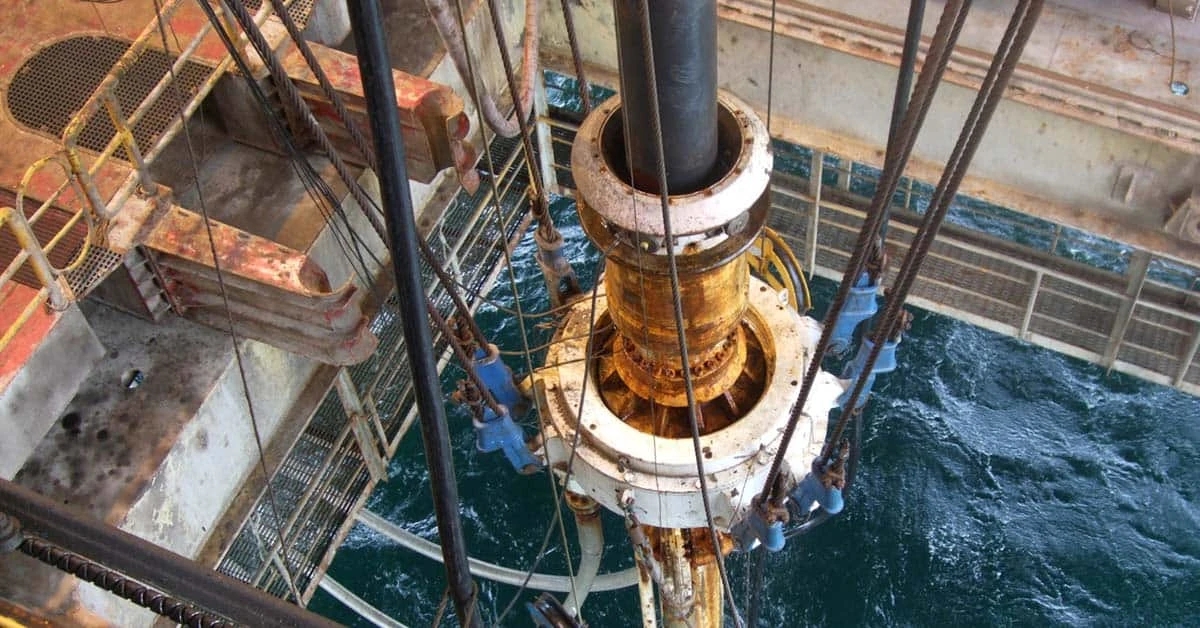
In engineering, it’s crucial to select materials that will resist corrosion – and monitor their performance
Caption: Corrosion failure on offshore drilling structures may result in near misses. (© istock.com)
As an engineer, you likely have several goals when selecting materials for equipment and infrastructure design. Safety and long-term reliability are critical. At the same time, you want to minimize material costs, avoiding both under- and over-specification.
To achieve these goals, you are weighing many factors. Considerations when selecting a material can include:
Physical properties
Corrosion resistance and galvanic incompatibilities
Mechanical properties
Ability of the material to be manufactured
Availability
Weight of materials
Lifecycle costs
Current or upcoming legislation
Compliance with standards
Approvals impacting the material
Previous experience with the selected material for a specific use
Of course, the relevance and prioritization of these considerations will vary from project to project, but all are necessary when beginning the materials selection process. The thing that keeps many engineers up at night is wondering what they might have missed, so it’s always best to be systematic as every possible factor is considered.
Knovel Corrosion, launched Sept. 30, 2021, will help safeguard equipment and reduce the $2.5 USD trillion annual global cost of corrosion.
Which materials cause corrosion — and which other factors should you consider?
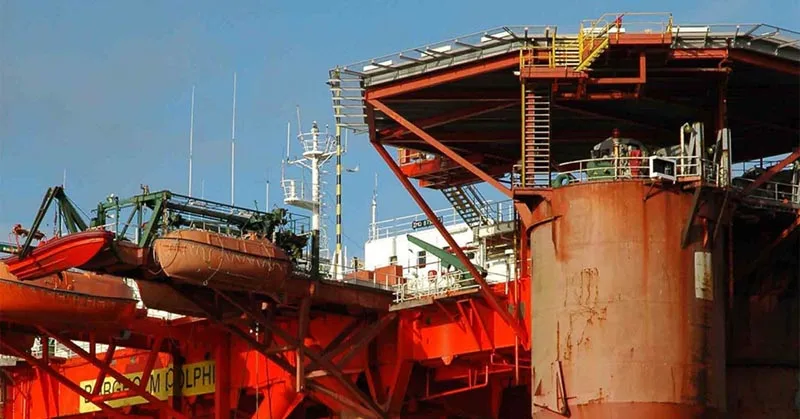
Exploration platforms encounter severe corrosion on components due to temperature, wind speed, salinity and humidity (© istock.com)
The tendency for a material to promote corrosion formation depends on both the composition of the material and the environment in which it is placed. It is never as simple as just avoiding certain materials. Instead, you have to consider what conditions your preferred materials might be exposed to, and whether the impact of corrosion is at acceptable levels. You’ll never be able to completely eliminate corrosion and other degradation, but you can manage it by better material selection and through the application of coatings, inhibitors and galvanic cathodic protection.
For example, in seawater applications, mild and stainless steels are subject to severe pitting and crevice corrosion; 6 Mo superaustenitic, 25 Cr superduplex or higher alloyed grades are required, such as 625 or 2507.
While investigating the impact of corrosion on materials, ready access to the following resources can help build confidence that reasonable materials are being selected for further review and testing:
Conditional corrosion rate data (temperature and concentration) for a range of environments and materials
Isocorrosion curves
Real-world case histories from practicing engineers in the field
Foundational guidance on corrosion management and material selection
Engineers also need to ensure that corrosion resistance is considered throughout fabrication, welding, installation and commissioning, which requires access to reference information specific to those stages.
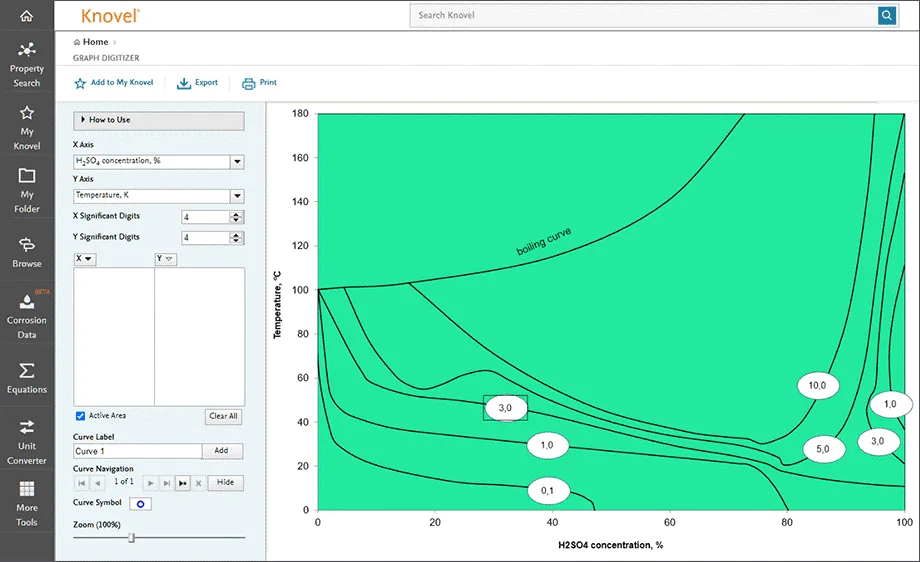
Isocorrosion curves from Knovel Corrosion helps understand the better resistance at higher concentrations and identify outlier conditions that will impact the relative resistance
A tool such as Knovel Corrosion can assist in identifying specific corrosion rates quickly with hundreds of interactive isocorrosion graphs.
Post-material selection monitoring is a must
You reviewed compatibility data, examined case studies, spoke with experts, ran tests, and made a smart material selection — but the job is not done. Monitoring corrosion post-selection is critical. It requires monitoring critical operating parameters, fluid flow, pH levels, etc. But what happens when these conditions change? How do you assess the corrosion resistance capabilities under the new operating parameters?
Oftentimes, equipment or piping is designed and manufactured for one particular function but ends up being used for a different purpose due to a process change (eg, processing a different crude oil), input change (eg, higher temperature or flow) and ongoing wear and tear. A change like this should trigger a reevaluation of material selection process.
An example from the oil and gas industry
A large integrated company operated several offshore production platforms in the Gulf of Mexico and had to delay hydrocarbon production due to corroded pipes, incurring associated costs of about $1 million.
Their engineer had to replace a 25-meter carbon steel pipe that carried produced water from a separator vessel. The produced water was corrosive due to acid gas formation and entrained solids, requiring the pipe to be replaced every four months and impacting production by 20 MBPD.
Using Knovel Corrosion, their engineer identified a particular alloy that withstood the highly corrosive environment and operated at the maximum CPT and CCT.
This change in material prevented the pipe from corroding as rapidly, saving the company roughly $1 million per year — plus the benefits of continuous production and increased safety.
Keeping corrosion away
Material selection is an ongoing process — you cannot “set it and forget it.” It’s important to weigh the options carefully and do all the necessary research in the initial selection to minimize the chance of corrosion problems down the line. Post-selection monitoring is also vital to ensuring materials continue to perform optimally.
This article was excerpted and adapted from Elsevier's white paper “Are you doing enough to get ahead of corrosion?” by Peter Nutty, C.Eng, and Matteo Caligaris, PhD.